Understanding Pulp System Equipment: Essential Insights for the Paper Manufacturing Industry
Release time:
2025-07-18
Pulp system equipment serves as a cornerstone in the paper manufacturing process, enabling the transformation of raw materials into usable pulp for paper production. Understanding its components, functionality, and significance can greatly enhance operational efficiency and ensure consistent product quality.
At its core, the pulp system is responsible for converting wood chips, recycled paper, or other fibrous materials into a slurry of pulp. This process involves several key stages, including pulping, screening, washing, and bleaching. Each of these stages requires specific equipment designed to optimize the extraction and purification of cellulose fibers.
One of the primary components of pulp system equipment is the pulper, which is used to break down raw materials into a slurry. There are various types of pulpers, including drum pulpers, hydropulpers, and continuous pulpers, each suited to different types of raw materials and production scales. Understanding the specific requirements of your production process can help in selecting the right type of pulper.
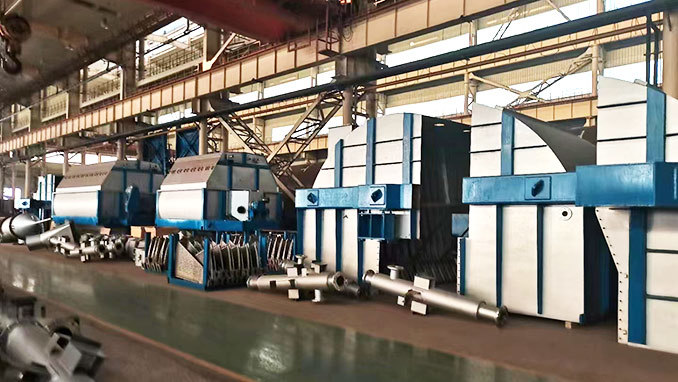
Screening equipment follows the pulping stage, removing contaminants and ensuring the pulp is of a suitable quality for further processing. This equipment typically includes deck screens and pressure screens, which help separate unwanted materials from the pulp, enhancing the quality of the final product.
Washing is another critical function of the pulp system, where impurities and excess chemicals are removed from the pulp. The washing stage can significantly impact the efficiency of the pulp production process, making washing equipment vital for maintaining product quality and minimizing environmental impact.
Bleaching equipment also plays a crucial role in achieving the desired whiteness and brightness in the final paper product. Various bleaching methods, such as chlorine dioxide, oxygen, and hydrogen peroxide, require specialized equipment designed to ensure optimal results while minimizing the use of harmful chemicals.
When discussing pulp system equipment, it is also important to consider the energy and resource efficiency of the machinery. Modern pulp systems are often designed with sustainability in mind, utilizing advanced technologies to reduce water and energy consumption, thereby lowering overall operational costs.
Moreover, regular maintenance of pulp system equipment is essential for ensuring longevity and optimal performance. Scheduled inspections and timely repairs can prevent unexpected downtime and maintain the efficiency of the manufacturing process.
In conclusion, understanding pulp system equipment is vital for any business engaged in the paper manufacturing industry. By familiarizing yourself with the various components and their functions, you can enhance operational efficiency, improve product quality, and contribute to a more sustainable production process. Consider investing time in evaluating the specific needs of your operation to make informed decisions regarding the equipment that will best serve your production goals.